2025.2.21
3Dプリント製造物の強度を高めるためのガイド
3Dプリント技術は、アイデアを形にする強力なツールとして、さまざまな分野で活用されています。しかし、3Dプリント製造物の強度について理解を深めることは、適切な応用シーンを見極め、最大の効果を得るために不可欠です。本記事では、3Dプリント製造物の強度に影響を与える要因やその改善方法について具体的に解説します。
1. 3Dプリント製造物の基本構造
1-1. 3Dプリンターの動作原理
3Dプリンターは、コンピューターで作成したデジタル設計データをもとに、材料を薄い層ごとに積み上げて形状を作りだす装置です。この方式では、層と層の結合が製造物の強度に大きく影響します。
たとえば、FFF方式(材料押出法)はノズルから溶融したプラスチック材料を押し出しながら積み上げる方式で、家庭用やプロトタイピングに広く利用されています。ただし、層間の接着が弱いと引張強度が低下することがあります。
SLA方式(光造形法)は液体樹脂をレーザーで硬化させる方式で、精細で滑らかな仕上がりが可能ですが、硬化後の材料が脆くなる場合があります。
SLS方式(粉末床溶融結合法)では、粉末状の材料をレーザーで焼結し、強度と複雑な形状の両立が可能です。高耐久性が求められる機械部品の製造に適しています。
MJF方式(材料噴射法)は、材料を層ごとに噴射し、詳細表現や滑らかな表面仕上げに優れています。
最後に、DED方式(指向性エネルギー堆積法)は、金属ワイヤーや粉末を高出力レーザーや電子ビームで溶融しながら、ノズルを移動させて積層する方式です。積層速度が速く、材料の無駄を最小限に抑えられるのが特徴です。
このように、それぞれの方式は得意分野や用途が異なるため、目的に応じて適切な方式を選ぶことが重要です。
1-2. 3Dプリントの設計プロセス
設計プロセスでは、特定の応力や荷重を受ける箇所に適切な補強を施す必要があります。たとえば、引っ張り力がかかる部分には円形断面を採用するか、リブを追加することで強度を確保できます。また、シミュレーションソフトを使用してストレス解析を行うことで、弱点を事前に補強することが可能です。
1-3. 造形における層の重要性
3Dプリントでは、積層高さ(レイヤー厚)や層の密着度が製品の強度に直結します。具体的には、層高さを低く設定することで層間結合を強化でき、結果として引張強度が向上します。積層ピッチを小さくすることで印刷物がより滑らかに造形できる一方、印刷時間が長くなるといった点も存在します。また、プリント方向に応じて異なる強度が得られるため、部品の最適な配置も重要です。
2. 3Dプリント方式別の強度向上ガイド
2-1. 材料押出法式(FDM/FFF)
FDM/FFF方式は、家庭用から工業用途まで広く使われており、比較的コストが低いことが特徴です。ただし、層間接着が課題となりやすく、積層方向に沿って割れやすい傾向があります。対策として、ナイロンやABSのような強度の高い材料を選び、エンクロージャーを使用して温度を一定に保つことが重要です。また、レイヤーの高さを細かく設定することで層間結合を向上させられます。
2-2. 光造形方式(SLA/DLP)
SLA/DLP方式では、液体樹脂をレーザーまたはプロジェクターで硬化させて造形します。造形物は高い寸法精度と滑らかな表面を持ちますが、硬化後の材料が脆いため、強い衝撃や引っ張り力には不向きです。UV硬化やエポキシ樹脂によるコーティングを施すことで、脆さを軽減し、強度を向上させることが可能です。
2-3. 粉末床溶融結合方式(SLS/SLM)
SLS方式はナイロン粉末などを用い、均一な強度を持つ部品を造形できます。層間強度が高く、複雑な形状でも高耐久性が求められる用途に適しています。一方、SLMは金属粉末を用いて、部品の剛性や耐熱性を確保します。この方式は航空機や自動車部品の製造で重宝され、高い機械的強度を必要とする場合に選ばれます。
2-4. 材料噴射方式(MJF/PolyJet)
MJF方式では、粉末材料に結合剤を噴射して造形します。表面仕上げが滑らかで、耐久性と詳細表現を両立させることができます。また、PolyJet方式ではインクジェット技術を利用して液体樹脂を精密に積層し、滑らかで複雑な造形が可能です。この方式は、柔軟なゴム状素材や硬い樹脂など、異なる材料を組み合わせて造形できる点が特徴です。高精度の造形が可能である一方、耐久性が必要な部品では追加の仕上げ加工や材料選択が求められる場合があります。
2-5. 指向性エネルギー堆積方式(DED)
DED方式は、金属材料をレーザーや電子ビームで溶融しながら堆積させる技術で、大型構造物の修復や製造に利用されます。この方式で得られる造形物は非常に高い強度を持ち、特に圧縮や剪断応力に優れています。航空宇宙分野では、破損部品の補修や新規部品の製造で重要な役割を果たします。
造形方式別メリット・デメリット
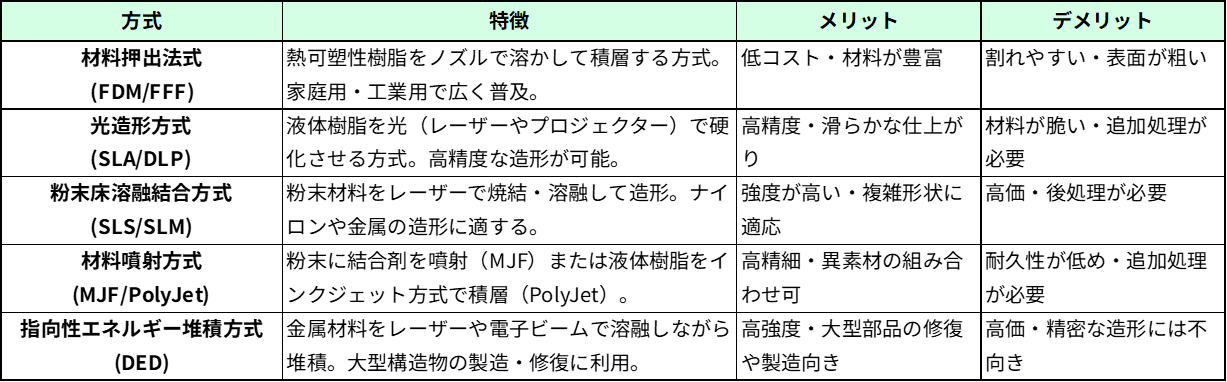
3. 3Dプリント条件が強度に影響を与える要因
3-1. 材料選びのポイント
高負荷がかかる部品にはカーボンファイバーや金属粉末混合材料を使用すると、従来材料の数倍の強度が得られます。また、熱や薬品にさらされる環境では、耐熱性や耐薬品性のある材料を選ぶ必要があります。
3-2. 強度が強い材料は?
強度を重視する場合、以下のような材料が選択肢として挙げられます
- カーボンファイバー強化フィラメント
プラスチック材料にカーボンファイバーを混合したフィラメントは、軽量かつ高剛性を提供します。特に耐荷重性が求められる部品や構造物に適しています。 - ポリカーボネート(PC)
耐衝撃性と耐熱性に優れた材料で、工業用途に広く利用されています。荷重のかかる部品に適した選択肢です。 - ナイロン(PA)
柔軟性と高い引張強度を持つ材料で、耐摩耗性にも優れています。機械部品や可動部に適しています。 - PEEK(ポリエーテルエーテルケトン)
高い耐熱性と機械的強度を兼ね備えたエンジニアリングプラスチックで、航空宇宙や医療分野で使用されています。 - 金属粉末材料
SLMやDED方式で使用される金属粉末(アルミニウム、チタン、ステンレス鋼など)は、最高レベルの機械的強度を提供します。特に圧縮や引張強度が求められる部品に最適です。
これらの材料を選ぶ際は、製品の用途や環境条件(温度、湿度、化学薬品への曝露など)を考慮することが重要です。
3-3. プリント条件とその影響
以下の条件が強度に大きな影響を与えます
- ノズル温度: 適切な温度設定で層間結合を強化します。
- プリント速度: 低速設定(40mm/s以下)は強度向上に有効です。
- 冷却ファン: PLAでは冷却が必須ですが、ABSでは控えめにすることで層間剥離を防ぎます。
3-4. 内部構造とフィルパターン
内部の充填率やフィルパターンを調整することで、軽量化と強度のバランスを取ることができます。
- 格子パターン: 等方的な強度を提供し、均一な荷重分散が可能。
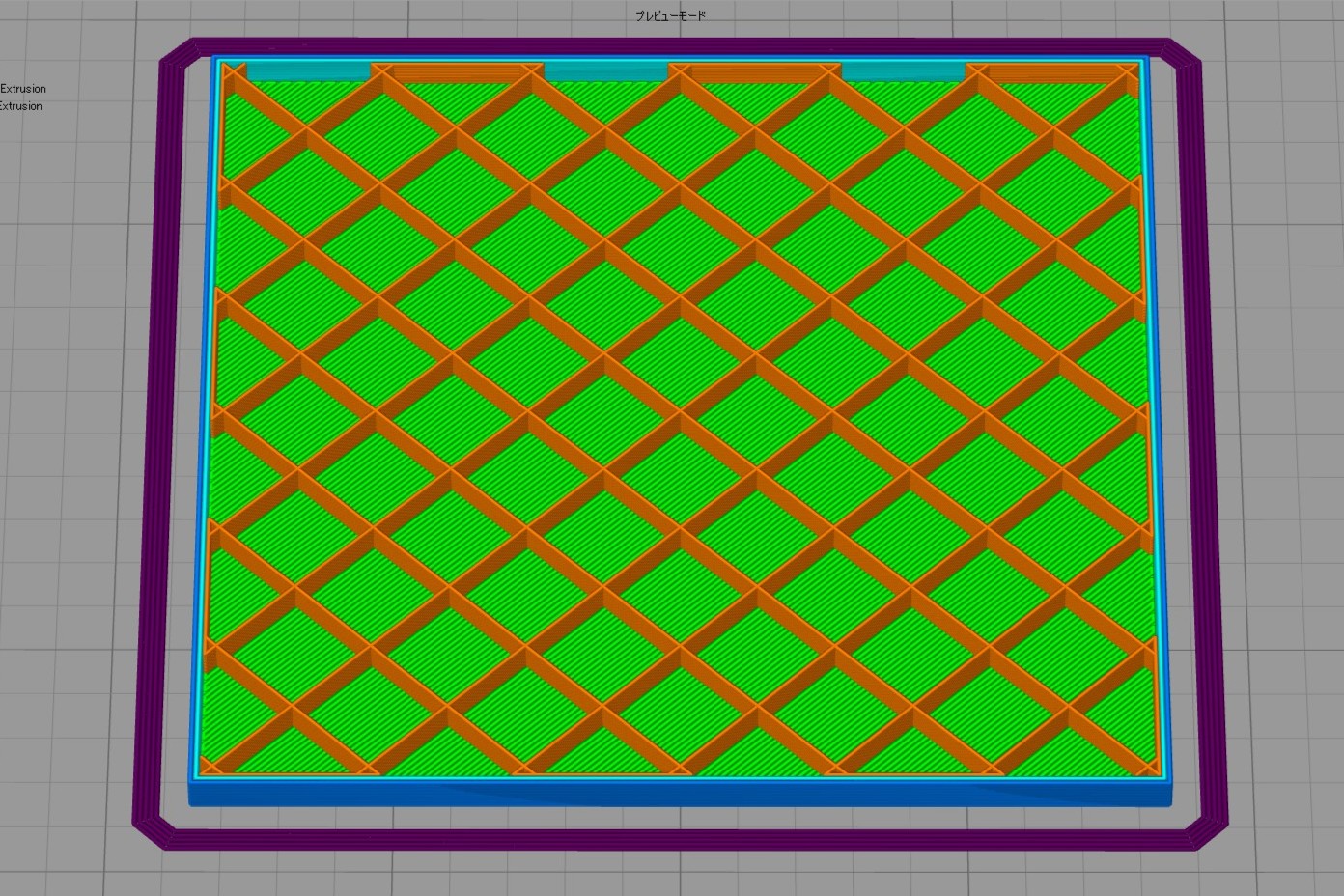
- 三角形パターン: 高い剛性を提供。
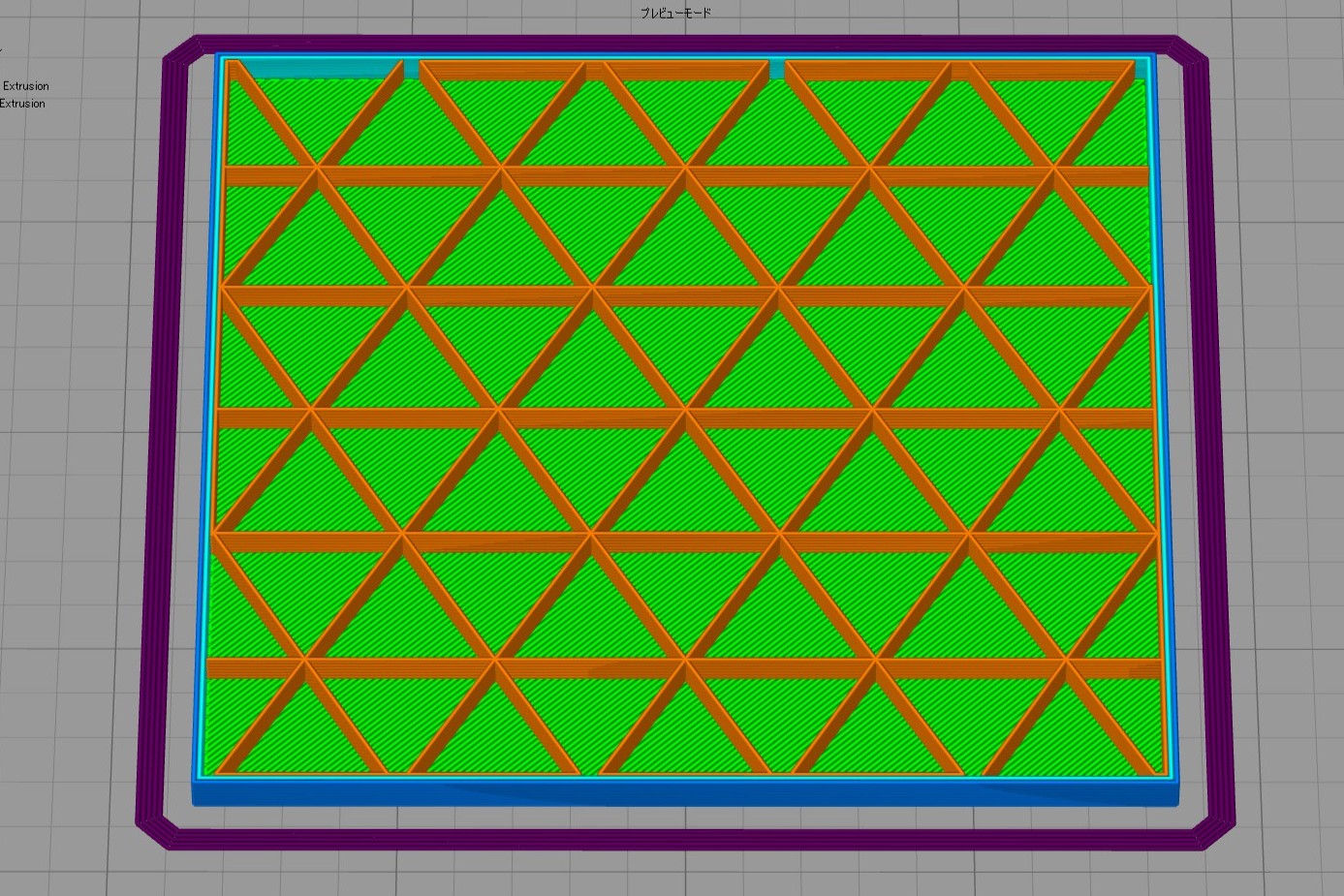
- ハニカムパターン: 軽量で耐荷重性に優れる
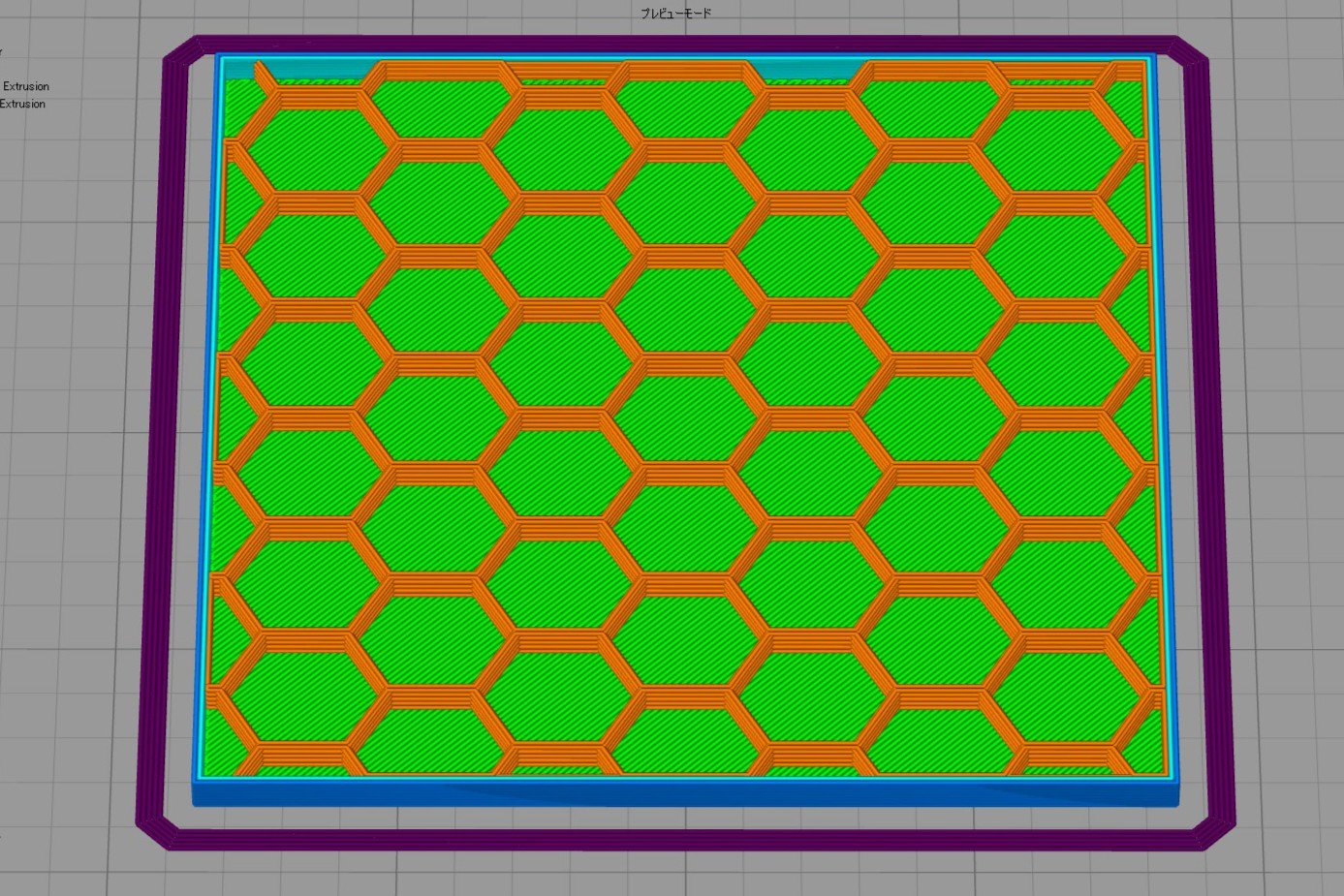
- ソリッドフィル: 最大強度が得られるが、材料消費と時間が増加。
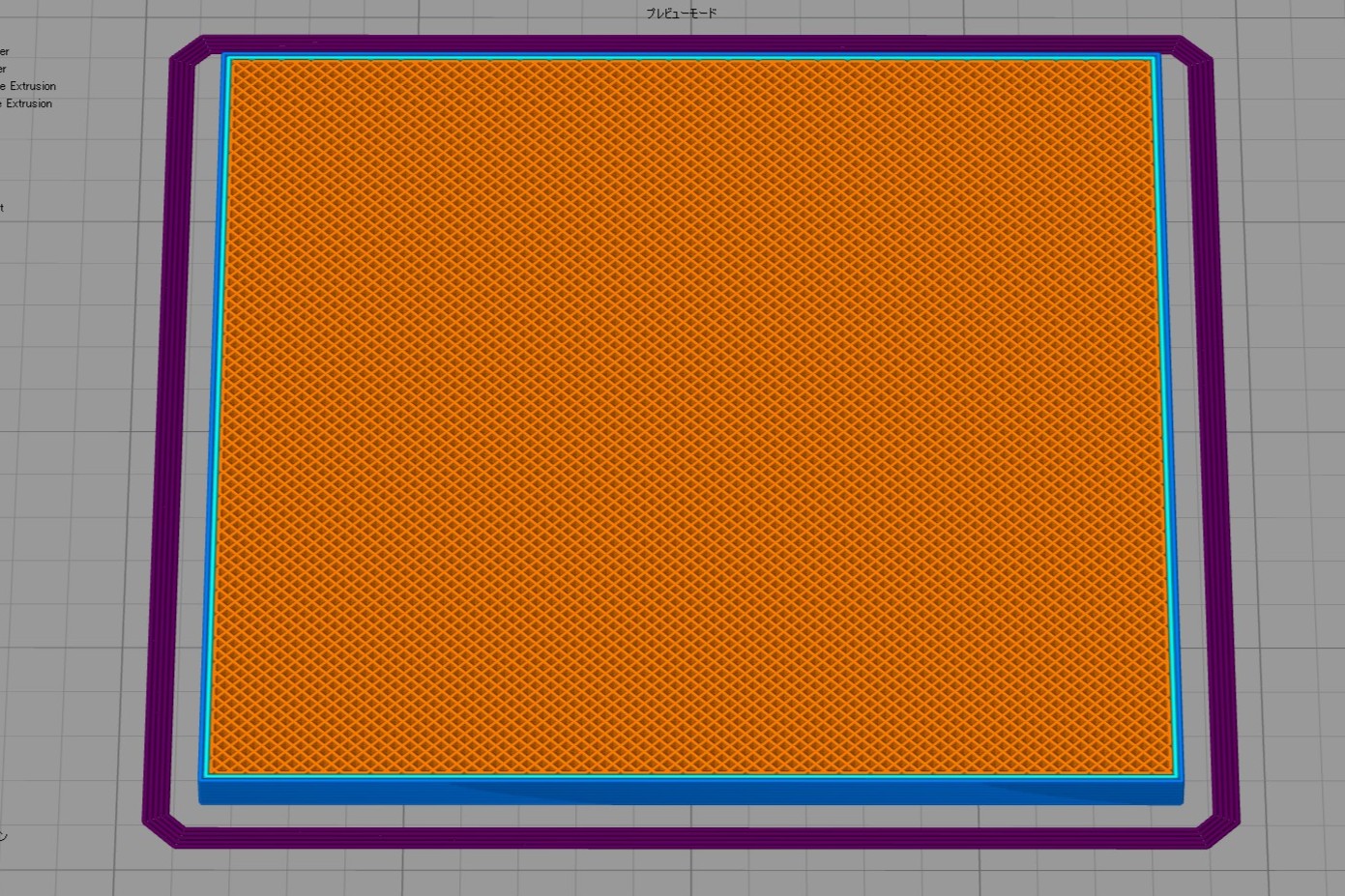
4. 強度を高めるための3Dプリンティング戦略
4-1. 設計段階での留意点
設計段階での留意点として、応力が集中する部位にはフィレット(曲面)を追加し、応力集中を軽減することが有効です。また、薄い壁構造にはリブを追加して剛性を向上させることが推奨されます。
4-2. 材料の強化と複合材料の利用
材料の強化には、カーボンファイバーやガラス繊維などのフィラメントを利用します。これらの材料は高価ですが、複合量を調節すると従来のプラスチックフィラメントに比べて2倍以上、アルミと同等の剛性を提供することもあります。
4-3. 最適なプリント設定の選択
設定を最適化することで、機械的特性を最大限に引き出せます。具体例として
- レイヤー高さ
小さいレイヤー高さ(0.1mm以下)は滑らかな表面と高強度を実現します。例えば、0.05mm以下の設定では、光造形方式のような非常に滑らかな仕上がりが可能となり、デザイン性を求める製品に適しています。一方、複合材料を用いた場合、カーボンファイバー強化PLAを使用することで、航空宇宙や自動車部品に適した高剛性部品を製造できます。 - 外壁ライン数
複数の外壁ラインを設定することで、外部からの衝撃に耐える構造が得られます。
4-4. ポストプロセスでの強化手法
ポストプロセスとして、熱処理を行うことで結晶構造を強化できます。また、ナイロン部品においては染色処理とともに耐久性を向上させることも可能です。
4-5. 後加工時にできる工夫
金属部品とのハイブリッド化や接着剤を使用した部品接合は、従来の3Dプリント製造では難しかった高負荷用途に対応します。
- FDM/FFF方式の場合
3Dプリント製品にねじ穴を設けたうえで、インサートナットやボルトを装着することで、トルクや応力に対する耐久性を向上させることが可能です。また、プリント後に接着剤を使用して複数部品を一体化する方法も有効です。 - SLA/DLP方式の場合
滑らかで高精度な表面を生かして、接着剤の接着面を確保しやすいのが特徴です。強化が必要な箇所には、金属ピンや補強材を埋め込む設計が適しており、応力集中を軽減できます。
5. まとめ
3Dプリント製造物の強度を最大化するには、材料選び、設計、プリント条件、仕上げ加工といった各工程での具体的な工夫が重要です。用途や要件に応じて適切な戦略を採用することで、3Dプリント技術の可能性を最大限に引き出すことができます。
弊社では用途や要件に応じた3Dプリントの活用が可能です。ぜひ一度ご相談ください。