2024.11.7
3次元水管によって、
射出成形の冷却時間を半減。
プラスチック製品業界において、広く普及している製造方法のひとつが射出成形。その工程は主に次の4つに分けられます。
その1「溶融プラスチックの射出」その2「金型内での圧縮」その3「冷却処理」その4「成形品を取り出す」。なかでもその3の「冷却処理」に全体の70~80%の時間が使われていると言われています。
そこに変革をもたらすゲームチェンジャーとして注目を集めているのが、3Dプリンターによって実現した3次元水管です。通常、複雑なプラスチック製品は、その曲面に直線上に穴の開いた冷却流路を沿わせることが困難。結果、冷却時間が長くなることで金型表面温度が均一でなくなり、製品の品質が低下。不良品につながってしまいます。
その画期的な解決策が3次元水管です。3Dプリンターによって、金型の形状やプラスチック製品の輪郭に沿って、より効率の良い冷却流路を精密に設計することが可能となりました。冷却時間が短縮されるだけでなく、金型表面温度の均一性を高め、冷却性能を飛躍的に向上させます。
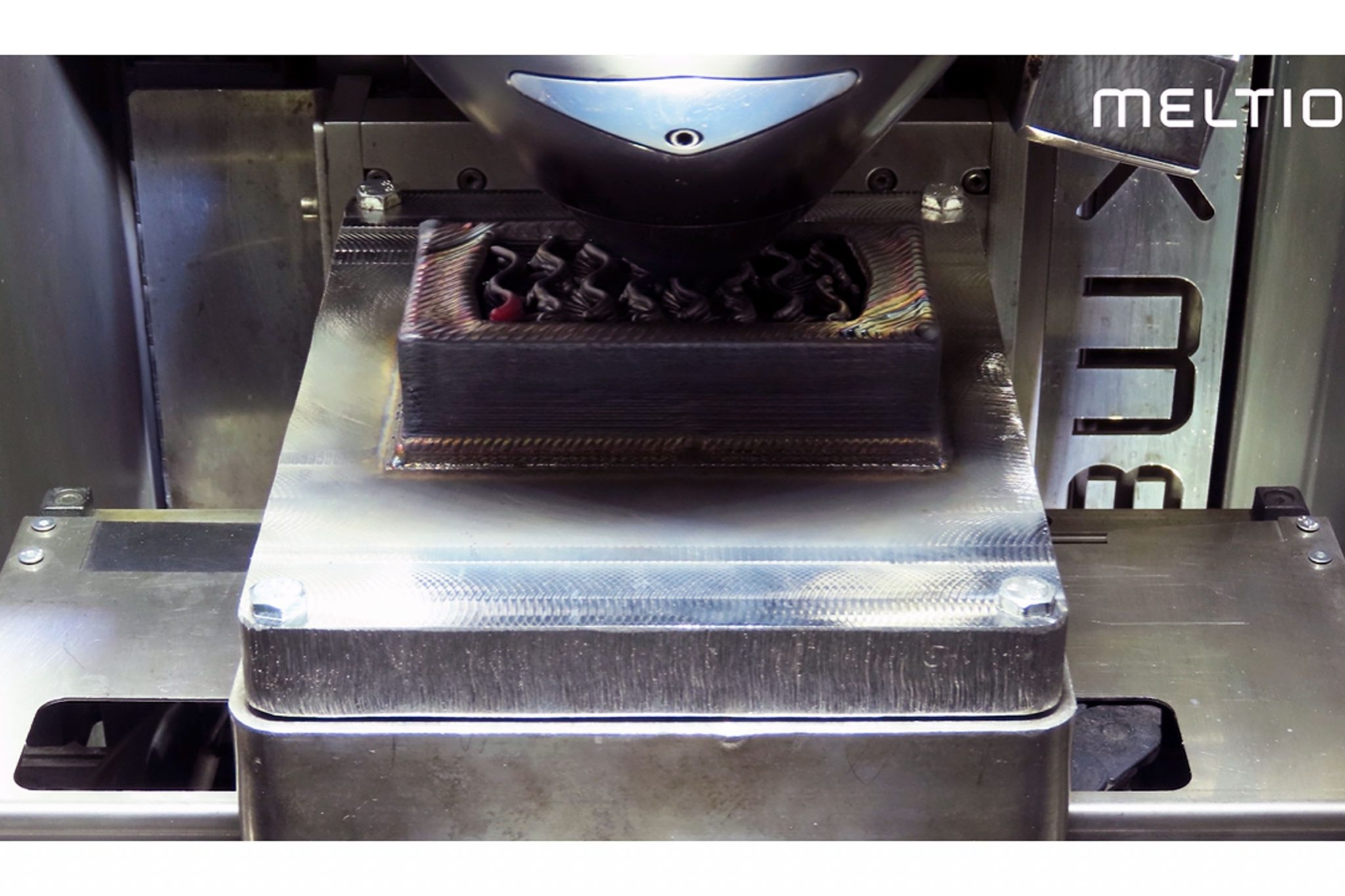
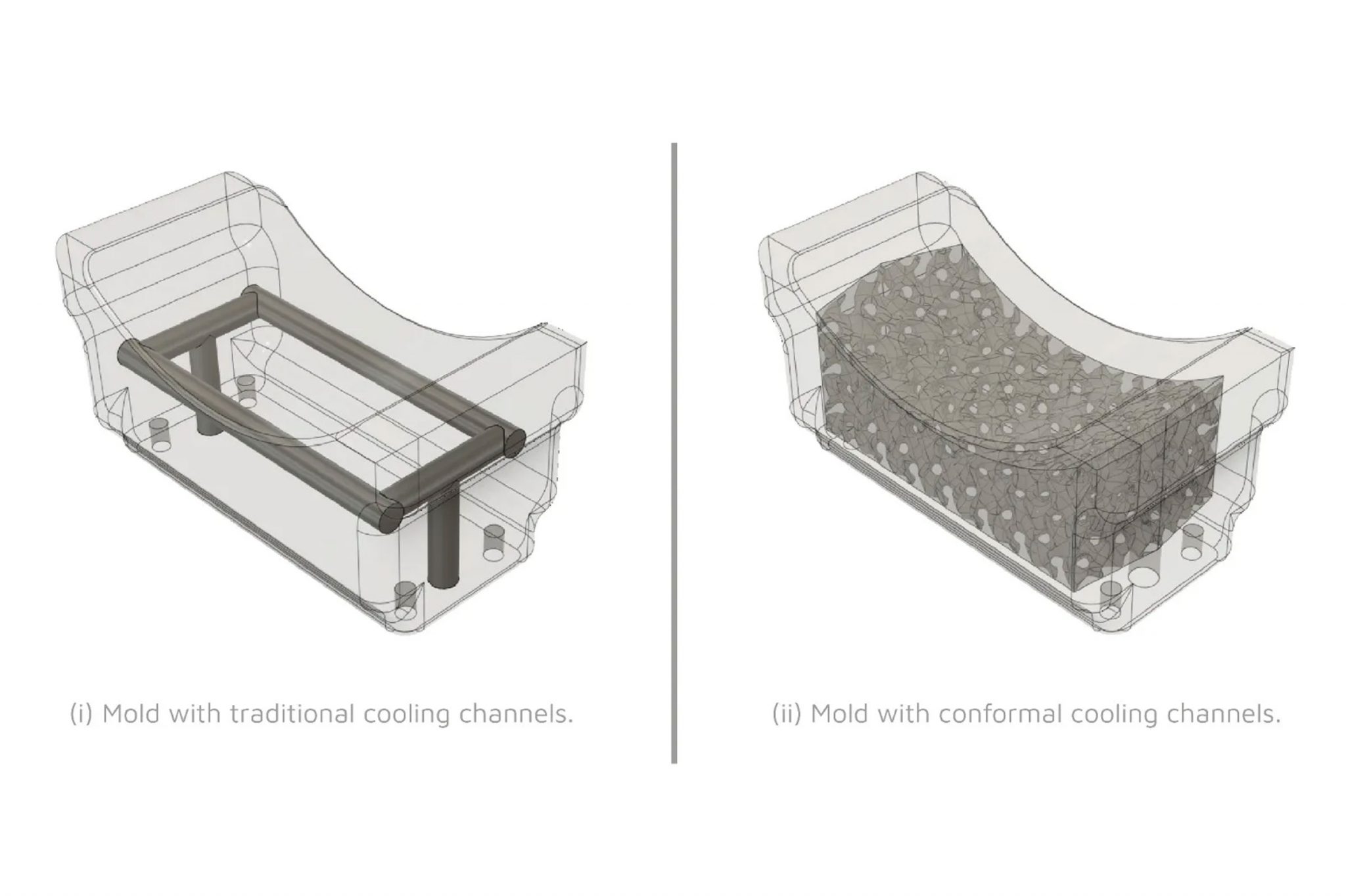
当社が採用するのはワイヤーDED方式金属3Dプリンター。格子構造からなる3次元水管を配置した射出成形金型の製造を可能にしました。格子構造は金型の全体的な構造的完全性を高めるだけでなく、射出成形工程での効率的な熱放散を促進。あわせて、正確な温度制御、成形サイクルの時間短縮、成形部品の品質と一貫性の向上を実現します。なおかつ、同プリンターが生み出す3次元水管を配置した射出成形金型は、従来の金型よりも安価。当社の検証においては、従来品と比較して冷却時間を約50%カット、成形利益率は約55%アップするという結果が出ています。
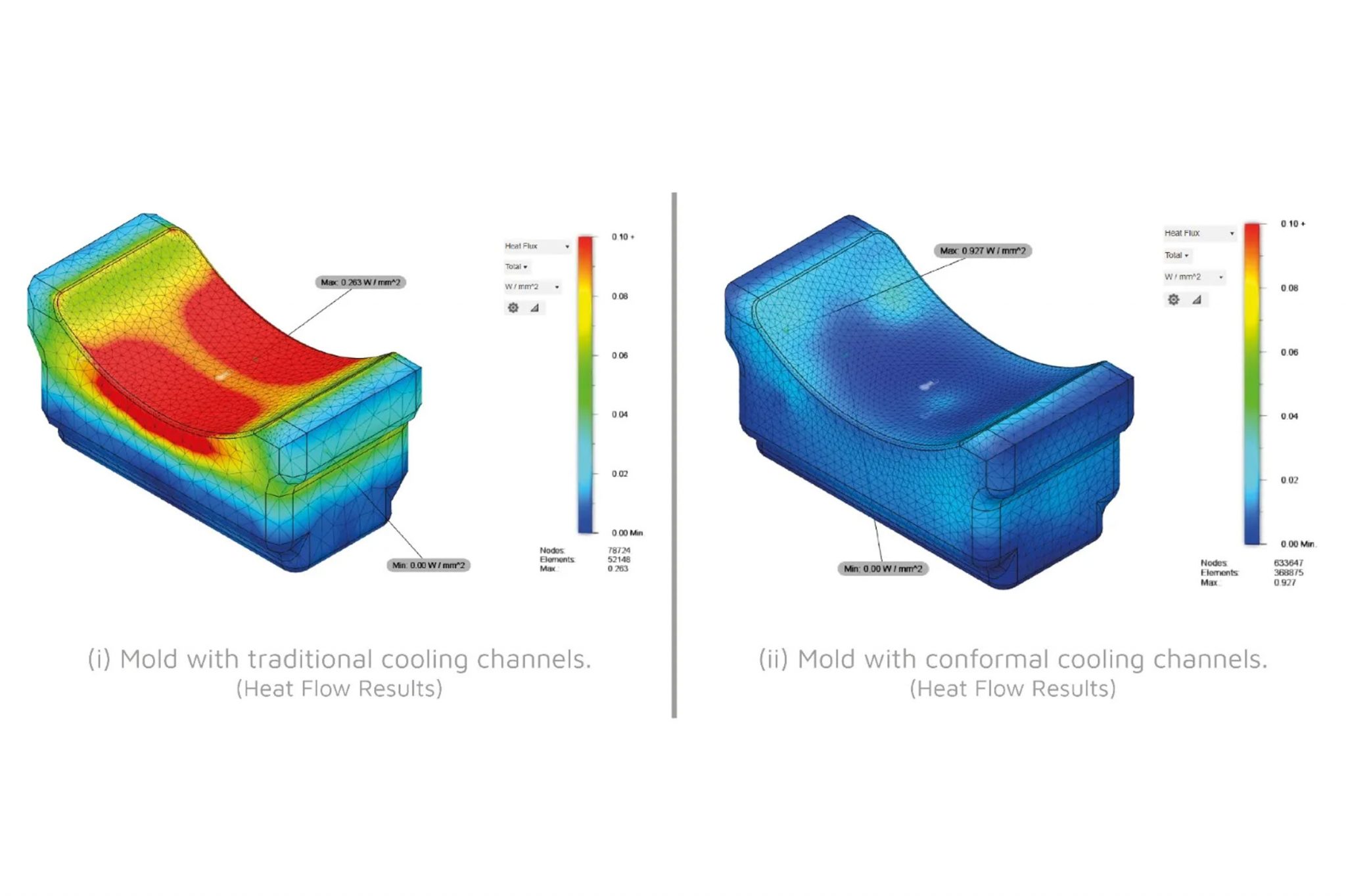
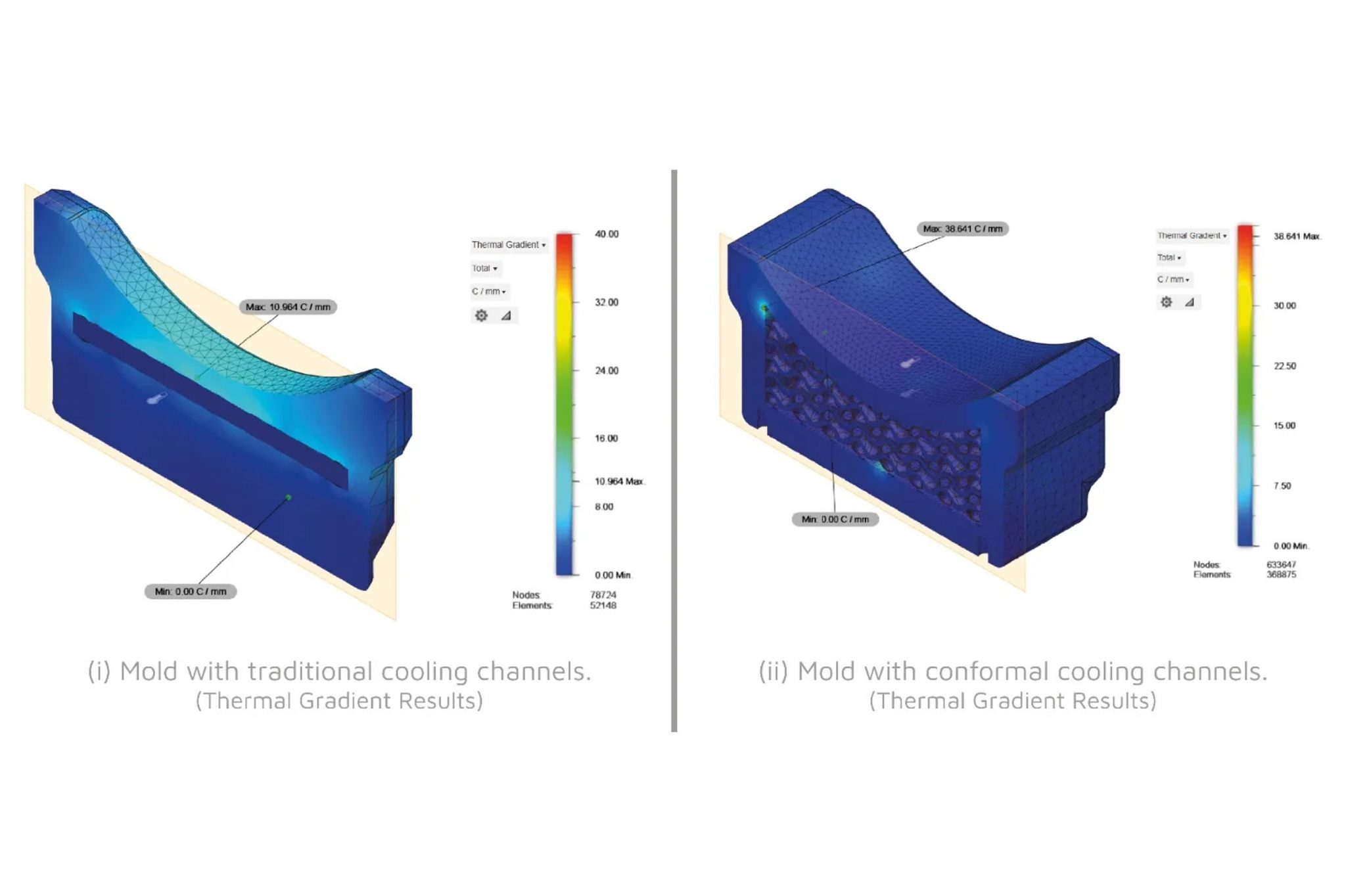
3Dプリンターだからこそつくれる3次元水管を配置した射出成形金型。御社のモノづくりを次のステージに引き上げる可能性を秘めています。ご興味あれば、お気軽にお問い合わせください。